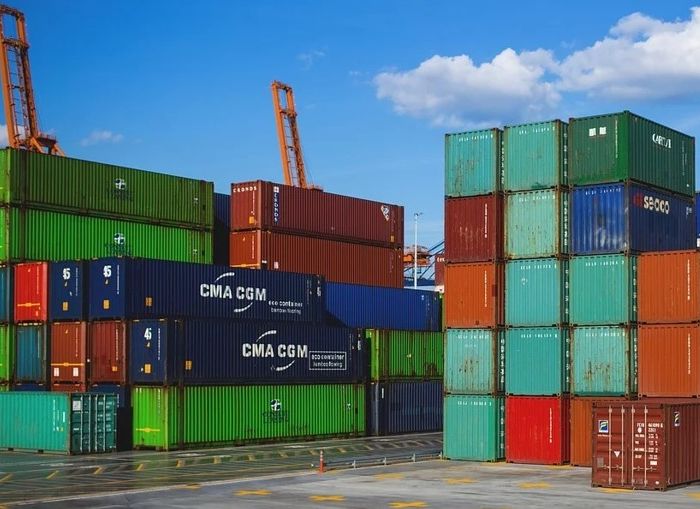
Manufacturing Footprint Optimierung
Abkühlende Konjunktur, volatile Märkte und unsichere politische Umfelder erfordern, dass international agierende Industrieunternehmen ihren Manufacturing Footprint hinterfragen. Nach einigen Phasen des Outsourcings und Insourcings stehen produzierende Unternehmen damit vor einer Welle von Verlagerungen, Verdichtungen oder Schließungen von Produktionsstandorten. Kostendruck und Margenerosion treiben den Optimierungsgedanken der Unternehmen und bringen damit ein komplexes und wegweisendes Projekt zur Produktionsoptimierung auf die Agenda des Managements: An welchem Standort soll zukünftig welches Produkt in welcher Menge produziert werden. Wie können so Kosten gesenkt, Maschinenauslastung erhöht und Produktionsprozesse beschleunigt werden können? Das Management benötigt dafür ein Instrument, dass schnell robuste und entscheidungsrelevante Ergebnisse bereitstellen kann. Es müssen Inputs aus allen Unternehmensbereichen vereint, zahlreiche Datenquellen angebunden, komplexe Wirkungsketten abgebildet und gleichzeitig eine flexible, dynamische Simulationslösung angeboten werden.
Für die Entwicklung eines Instruments zur Entscheidungsunterstützung bei Manufacturing Footprint Optimierungen hat sich folgendes Vorgehensmodell, das sich in drei Phasen untergliedern lässt, bewährt. Die drei Phasen, die Klärung der strategischen Eckpunkte, die tatsächliche Simulation der Optionen sowie die Unterstützung in der Umsetzung werden im Folgenden detailliert beschrieben.
Abbildung 1 Vorgehensmodell zur Manufacturing Footprint Optimierung
1 Klärung der strategischen Fragestellung
Entwicklung und Evaluierung von entscheidungsrelevanten Szenarien
In einem ersten Schritt werden gemeinsam mit dem Management die grundlegenden strategischen Stoßrichtungen erarbeitet und Leitplanken für die weitere Definition der Szenarien festgelegt. Folgende Fragen werden gemeinsam diskutiert und daraus Handlungsspielräume abgeleitet:
- An welchem Standort soll zukünftig welches Produkt in welcher Menge produziert werden?
- Was ist die minimale Produktionsauslastung für einen Standort, wie wird mit Standorten umgegangen, die diese unterschreiten?
- Durch die Zusammenlegung welcher Produkte und Produktionsprozesse können Synergien gehoben und dadurch Kosten eingespart oder Abläufe beschleunigt werden?
- Wie viele Reserven müssen in den Standorten für Auslastungsspitzen gegeben sein, um flexibel auf Nachfrageschwankungen reagieren zu können?
- Welche sozialen Auswirkungen hat eine Verschiebung von Produktionsmengen / die Erweiterung oder auch Schließung von einzelnen Werken?
- Welchen finanziellen Effekt haben diese Maßnahmen zur Optimierung des Manufacturing Footprints?
Für die Ableitung der entscheidungsrelevanten Szenarien wird ein interdisziplinäres Projektteam benötigt, das insbesondere die Bereiche Vertrieb, Produktion und Controlling abdeckt. Dabei werden neben der qualitativen Beschreibung auch die zentralen Annahmen zu Markt- und Standortentwicklung festgehalten. Im Zuge dessen sollten stets die für die Entscheidung relevantesten Szenarien priorisiert werden. Ebenfalls ist es wichtig zu diesem Zeitpunkt eine Baseline (Vergleichsszenario) zu fixieren. Dafür können Budget und Mehrjahresplanung herangezogen werden.
Festlegung Bewertungskalkül
Um die unterschiedlichen Szenarien vergleichen zu können, muss ein einheitliches Bewertungskalkül für die Entscheidung festgelegt werden. Dabei sollte auf ein Set von unterschiedlichen Kennzahlen zurückgegriffen werden, welches aus dem Steuerungsmodell des Unternehmens abgeleitet wird. Dieses Set umfasst sowohl finanzielle Kennzahlen (z.B.: Kapitalwert, EBIT, EBITDA, Investitionen, Einmalkosten, Personalkosten, …) als auch nicht-finanzielle Kennzahlen (soziale Verträglichkeit (Mitarbeiter), Personalauslastung, Maschinenauslastung, Produktionsmengen ,…).
Ableitung der wesentlichen Treiber und Einflussgrößen
Auf Basis der strategischen Fragestellungen und dem Bewertungskalkül müssen die wesentlichen Treiber und Einflussgrößen erarbeitet und definiert werden. Das können zum Beispiel Produktionsmengen, Produktionskapazitäten, Bearbeitungszeiten, Personalstunden, Arbeitsplätze oder Produktionsflächen sein. Aus Vertriebssicht sind ebenfalls Nachfragemengen, Produktmix, Lieferzeiten oder auch Qualitätskriterien relevant.
Auf Basis dieser Ergebnisse kann mit der Entwicklung eines dynamischen Simulationsmodells begonnen werden.
2 Evaluierung in einem dynamischen Simulationsmodell
2.1 Aufbau & Entwicklung
Simulationslogik
Um die gesamte Tragweite von Produktionsverschiebungen / -verlagerungen simulieren zu können, muss das Tool Inputs aus verschiedensten Themengebieten berücksichtigen können:
- Produktionsmengen und -auslastungen (Maschinen, Personal, Fläche)
- Produkt (Arbeitspläne, Stücklisten, Kalkulationen)
- Infrastruktur (Maschinen, Produktionsflächen, Lagerflächen)
- Personal (Freisetzungen, Umschulungen, Aufbau, Kollektivverträge)
- Marktnachfrage (auf Märkte und Produkte aufgeteilt)
- Materialeinkauf (Mengen, Verfügbarkeit, Lieferantenbedingungen)
- Finanzierung (Kredite, Zinskonditionen)
- Logistik (Lieferbedingungen, Lieferzeiten, Zölle, Transportkosten)
- Projektabwicklung (Projektmitarbeiter, Rechts- & Beratungsaufwände, Reise- und Schulungskosten)
Die verwendete Simulationslogik muss sicherstellen, dass die Abhängigkeiten all dieser Variablen korrekt abgebildet sind, damit die daraus resultierenden finanziellen und nicht-finanziellen Effekte ermittelt und ein kohärentes und eindeutiges Ergebnis abgeleitet werden kann. Da die Handlungsalternativen oft aus mehreren Maßnahmen bestehen, ist eine dynamische Kombination unterschiedlicher Maßnahmen ein weiterer Entwicklungsschritt, der den Entscheidungsfindungsprozess wesentlich verbessern kann.
Iteratives Vorgehen
Gemeinsam mit dem interdisziplinären Projektteam werden anschließend die einzelnen Szenarien befüllt, simuliert und bewertet. Die definierten Annahmen der unterschiedlichen Szenarien werden ins Modell eingepflegt und um weitere Details ergänzt. Danach werden die Zahlen in einem iterativen Prozess vom Projektteam validiert, um möglichst robuste und realistische Ergebnisse zu erzeugen. Gleichzeitig kann dadurch ein erhöhtes Buy-In des Projektteams erzielt werden.
2.2 Herausforderungen im Entwicklungsprozess
Im Zuge des Aufbaus und der Entwicklung eines dynamischen Simulationsmodells gilt es, Zielkonflikte zwischen Flexibilität der Simulation, maximaler Detailtiefe, finanzieller Integrität und tatsächlicher Datenqualität zu managen. Folgende Überlegungen sollten daher möglichst früh in den Entwicklungsprozess einfließen:
- Flexibilität der Simulation: Grundsätzlich gilt, je mehr Variablen simuliert werden können, desto leichter lassen sich unterschiedliche Szenarien abbilden, d.h. das Modell ist sehr flexibel. Diese Flexibilität hat aber ihren Preis: es müssen sehr viele Daten für jede mögliche Kombination der Simulation gesammelt werden, die Komplexität und der Wartungsaufwand der technischen Lösung steigt und möglicherweise muss auf Detaillierungsebenen verzichtet werden. Entscheidend ist also die Lösung soweit flexibel zu gestalten, wie es die Unterschiede in den Szenarien erfordern.
- Finanzielle Integrität: Wenn Produktionsmengen zwischen Standorten verschoben werden, müssen die Auswirkungen auf Gewinn- und Verlustrechnung, Cashflow und Bilanz integriert simuliert werden. In der Praxis treten Differenzen zwischen den Produktkalkulationen und den Periodenabschlüssen der Standorte auf. Daher werden manuell Korrekturpositionen benötigt, um gewisse Abweichungen berücksichtigen zu können. Finanzielle Integrität ist erfolgskritisch, um Fehlentscheidungen zu vermeiden, welche auf falschen Simulationsergebnissen basieren.
- Datengrundlage: Insbesondere bei system- oder länderübergreifenden Standortanalysen ist eine harmonisierte Datenbasis in der Praxis nicht immer vorzufinden. Die Daten müssen daher analysiert und gegebenenfalls angepasst (harmonisiert) werden. Ebenfalls ist eine externe Validierung von manchen Einflussfaktoren empfehlenswert (beispielsweise Mitarbeiter-Effizienz), um mögliche Verzerrungen aus internen Daten zu vermeiden.
- Detaillierungsgrad: Grundsätzlich gilt, das Modell darf nur weiter detailliert und „aufgebohrt“ werden, solange qualitative Inputs zur Verfügung stehen und steuerungsrelevante Outputs generiert werden können.
2.3 Ergebnis der Simulation (Simulationscockpit)
Sind alle Details zu den einzelnen Szenarien erarbeitet worden und sind die Ergebnisse für das Projektteam schlüssig, können die unterschiedlichen Szenarien anhand der finanziellen und nicht-finanziellen KPIs im Simulationscockpit verglichen werden. Dabei sollten die wichtigsten Kennzahlen in passenden Diagrammen aufbereitet sein. Gemeinsam mit den festgehaltenen qualitativen Vor- und Nachteilen der Szenarien und einer eindeutigen Empfehlung für eine (oder auch keine) dieser Alternativen, bilden diese Informationen die Entscheidungsgrundlage für das Management.
Zusammenfassend zeigt Abbildung 2 den groben Aufbau eines Simulationsmodells zur Entscheidungsunterstützung für Manufacturing Footprint Optimierungen. Neben den Basis-Inputs werden separat Maßnahmen ermittelt und bewertet. Über ein Steuerungscockpit lassen sich diese Maßnahmen kombinieren und über Szenarien ermitteln. Die Ergebnisse der Maßnahmenkombinationen lassen sich unmittelbar in übersichtliche Auswertungen überführen und unterstützen somit die Diskussionen im Management.
Abbildung 2 Modellaufbau
3 Überführung in operative Maßnahmen und laufendes Monitoring
Auf Basis dieses Ergebnisberichts trifft das Management eine Entscheidung für eine der möglichen Alternativen. Danach gilt die Aufmerksamkeit der internen und externen Kommunikation, besonders wenn Werkschließungen oder der Abbau von Mitarbeitern bevorsteht.
Überführung in operative Maßnahmen und Arbeitspakete
Im nächsten Schritt wird die gewählte Strategie weiter auf Standort- bzw. Fachbereichsebene hinuntergebrochen. Dafür werden operative Maßnahmen, inklusive Verantwortlichkeiten, Zeitpläne und Budgets, in Rücksprache mit den Standortleitern und den jeweiligen Fachbereichen, erarbeitet. Diese bilden die Grundlage für das weitere Maßnahmencontrolling.
Laufendes Monitoring
Um zeitgerechten Projektfortschritt und eine nachhaltige Optimierung des Manufacturing Footprints sicherzustellen, sind laufendes Monitoring und Controlling sowie eine aktive Projektsteuerung unumgänglich. Durch die unternehmensweiten Auswirkungen des Projekts sind eine Vielzahl an Standorten, Abteilungen und Personen involviert, was ein übergreifendes Projektmanagement erfordert. Oft scheitern diese Projekte an ihrer Komplexität (getrieben durch die vielen unterschiedlichen Akteure und die multidimensionalen Wechselwirkungen der Maßnahmen) und früher Euphorie folgt eine langsame oder unvollständige Umsetzung, welche es verfehlt Synergien zu heben und die Standorte nachhaltig aufzustellen. Eine externe professionelle Begleitung dieses Prozesses kann maßgeblich zu einem zeitgerechten Projektabschluss und einem wertsteigernden Ergebnis beitragen.
4 Fazit
Um die Optimierung des Manufacturing Footprints erfolgreich voranzutreiben, benötigt das Management ein geeignetes Tool, das schnell valide Entscheidungsgrundlagen liefert. Aufgrund der hohen Komplexität der Fragestellungen, müssen frühzeitig Mitarbeiter, Ressourcen und Kapital investiert werden, um diese zu bewältigen. Die unternehmensweiten Auswirkungen einer Manufacturing Footprint Optimierung sind nicht zu unterschätzen.